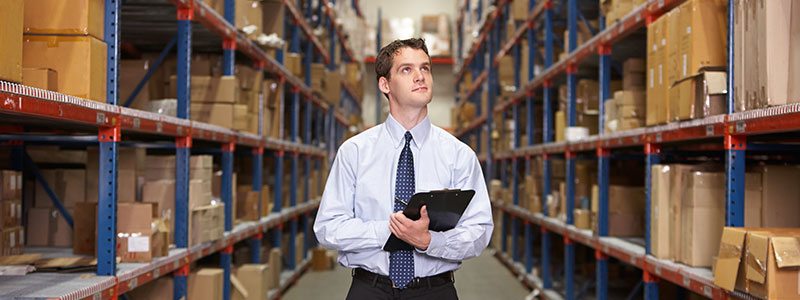
If you manage a warehouse, you may have come into an already established inventory system. That system may, or may not be, the best one for you to use based on industry, warehouse size and many other factors. Your business goals may dictate a change as well. Just because everyone else in your industry may use one style, that does not mean that a different method may not work best for you – and give you a competitive edge.
After all, the goal is to have your products where they need to be, when they need to be there, and do that better than the competition. Logistics aside, warehouse management comes into play first. So what is the best way to make that happen?
Inventory Method
First, pick an inventory method. Best known for its accounting ramifications, first in first out (FIFO) and last in first out (LIFO) are key inventory management decisions as well. As the name describes, for FIFO the first stock to come into the warehouse is the first to go out meet purchase orders and customer demand, while the last stock in is the first to go out in LIFO systems.
FIFO is the best option when shelf life of your product matters. If you sell milk, for instance, you are going to want to keep the oldest stock up front so that customers and order pickers choose that first, otherwise it will go bad. There are similar considerations for fashion, technology and other product lines where time is money.
LIFO works best when you manufacture your own products, so you can put the cost of goods to the sales in the appropriate time frame. You paid the most for the ones you made most recently so getting them out the door is priority to show real-time results. And if shelf life doesn’t matter, the monetary effect certainly does.
Inventory Setup
Your organization may have one warehouse, or several, in which product is kept and stored until purchased. Take a step back and figure out if it is best for each warehouse to have something of every product line, or to keep specific product lines in specific locations for better shipping, for example. There may other reasons – size of facility, type of storage needed, trucking routes – that dictate other plans but it is worth the discussion.
Once it is established which product lines will be in which warehouse, then look inside your four walls to figure out the best product placement. Most popular items in the front or along high traffic routes for easy picking? Are there ways to automate picking, or make it easier through the use of conveyors or push back / drive through pallet rack system options?
Assign locations so that staff knows where to put items when they come in and where to find them to fill orders. Set up a schedule of random inventories to confirm product numbers and catch mistakes early. Develop a clear documentation system as well, as that will save time later, and make it policy that all paperwork is dealt with as it comes in or needs to go out with an order. A mountain of paperwork slows everything down.
When you are using the right inventory setup from top down, your organization will find efficiencies and that edge that will keep you ahead of the opposition.