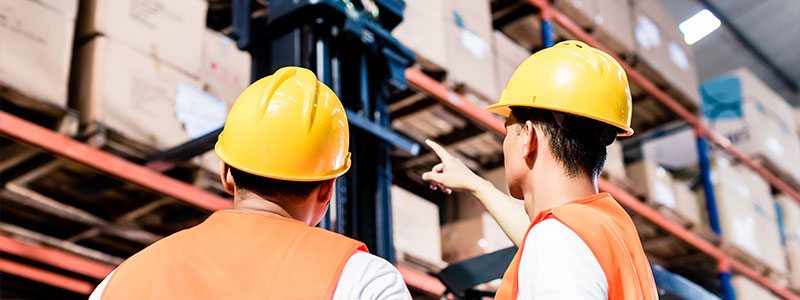
Time management is one of the most crucial factors in properly managing your warehouse. Time dictates how much product you are able to move, how efficient your workers are, the amount of money you bring in and pay out, and even has to do with the satisfaction of your customers. In the end, wasting less time almost always means bringing in more money. When it comes to inventory management, a good strategy is to place a timer on your processes. This way you can determine the value of each item which leaves your warehouse. Here are three timetables to help you determine the value of your products.
Time It Takes To Order Supplies. Companies constantly need to work with suppliers no matter if they manufacture their own products or get their merchandise from other manufacturers. As you are one of these companies, you need to take into account the flow of products coming in to your warehouse.
In order to have a good relationship with your supplier, you need to have established a reliable lead time or time it takes to replenish inventory. You should have a regular schedule when you expect your inventory to arrive and you should establish a good working relationship along with good communication with your supplier.
Time Inventory Sits. Inventory which sits too long can create problems. If you are working with perishable products, items which have been sitting a long time become unsellable. In instances like this, the loss of money becomes immediately apparent. However, sometimes products which merely take up space on shelves for too long cost you money.
The use of barcode scanners in your business can help combat the problem associated with inventory which sits too long. Having items scanned and in a system makes it easy to find products which have been sitting for a long time, even if they are pushed to the back of a shelf.
Distribution Timelines. After you determine how long it takes to get a product and find a buyer for that product, you need to determine how long it takes to actually get the item to the customer. There are multiple facets which go into this timeline including picking the product, preparing the order, and shipping.
Use mobile data collection devices to keep track of these processes. This way when workers are walking around the warehouse and picking items, they are collecting data in real time. You can then immediately view that data to see how efficiently your warehouse is operating and sticking to its timelines.